WORK-HOLDING FIXTURES
We are Japan’s premier manufacturer of vacuum work-holding fixtures for fuselage panels, and were the first manufacturer in Japan to utilize this cutting edge method of manufacturing aircraft skin. We work with our customers to design and custom manufacture these fixtures in a variety of sizes (up to 8m), shapes, and materials to suit their specific needs. Clamps, vacuum work holding, and other features can be included to create the perfect fixture for any machining job, including aircraft skin, CFRP panels, and precision parts. Our fixtures have been used by our customers in the manufacture of parts for the MRJ, Boeing 787, 777X, 777, and 767.
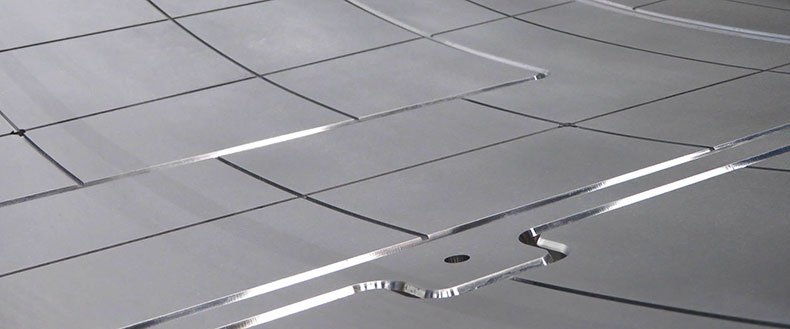
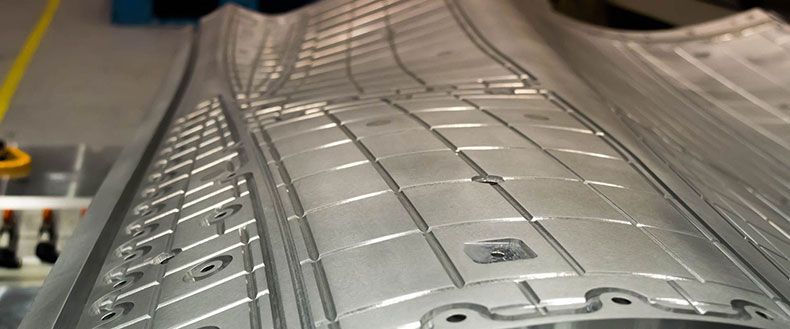
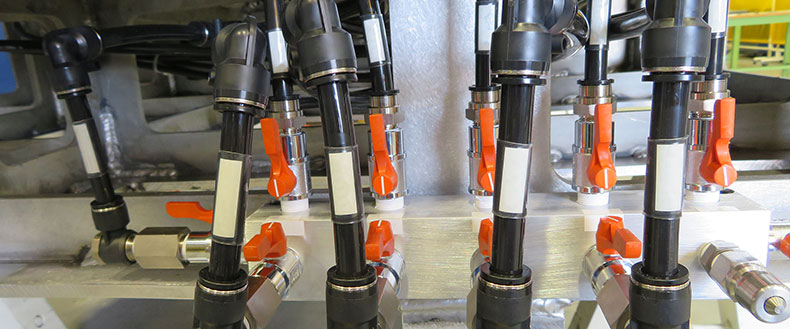

BENEFITS
Traditional methods for producing aircraft skin panels involve chemical milling; an expensive, time consuming, environmentally unfriendly process. The industry is moving towards mechanical milling, especially for processes such as aircraft skin thickness reduction. Our horizontal, shape specific fixtures provide the exact shape, precise fit, and vacuum workholding necessary at a fraction of the cost of other systems. Rather than investing in a multi-million dollar universal holding fixture, get the right tool for the right job the first time.
Compared to chemical milling, mechanically-milled panels can be manufactured 10 times faster and up to 50 percent cheaper, and the only by-product is aluminum shavings, which are completely recyclable.
As opposed to a specialized horizontal milling process, which requires expensive machines and fixtures to suspend the part, our fixtures allow panels to be manufactured by existing 5-axis machining centers, reducing capital costs by preventing the purchase of single use machines.